1. Multi-channel synchronous acquisition: Build a dynamic profile of the flow field
The flow field inside the turbine has transient and non-uniform characteristics, and it is difficult for traditional single-point pressure sensors to capture its dynamic changes. For example, the WindtunerEthernet Intelligent Pressure Scanners integrates 16 independent pressure channels and, in combination with a 500Hz channel sampling frequency, can synchronously collect pressure data from key parts such as turbine blade channels, combustion chambers, and exhaust ducts. For example, in the study of the flow heat transfer characteristics of the turbine casing of an aero engine, this device, through multi-channel networking technology, achieved the measurement of the instantaneous pressure distribution at hundreds of measurement points, providing high spatiotemporal resolution data for the analysis of aerodynamic loads on the surface of turbine blades.
Its advantage lies in the fact that the sensor is compatible with the IEEE1588 precision time synchronization protocol, ensuring that the timestamp error of data in each channel is less than 1μs. This millisecond-level synchronization capability enables engineers to precisely reproduce the entire process pressure changes of the turbine from startup to steady-state operation, providing a quantitative basis for optimizing the aerodynamic profile design of turbine blades. This means that when multiple physical quantity data such as pressure, temperature and vibration need to be collected simultaneously in the experiment, all the data can be precisely aligned under a unified time coordinate, laying the foundation for subsequent correlation analysis. This synchronous ability is particularly important for studying the complex fluid-structure coupling phenomena inside turbines, enabling researchers to precisely reconstruct the causal relationships among various physical quantities.
2. Intelligent diagnosis and adaptive calibration: Enhance test reliability
The test environment for turbines is complex. Factors such as high temperature, high pressure and vibration can easily cause sensor drift. The WindtunerEthernet Intelligent Pressure Scanners device, through its built-in zero calibration, full-scale calibration and custom multi-point calibration functions, combined with a digital temperature compensation algorithm, keeps the measurement error within ±0.05%FS.
In the durability test of a certain type of gas turbine, this equipment continuously monitored the surface pressure changes of the turbine blades for 2,000 hours through the regular automatic calibration function, successfully identifying the abnormal pressure distribution caused by carbon deposits, which was more than ten times more efficient than the traditional manual inspection. In addition, its safety protection level and shock-resistant design can resist the vibration and noise interference of the test bench, ensuring long-term stability.
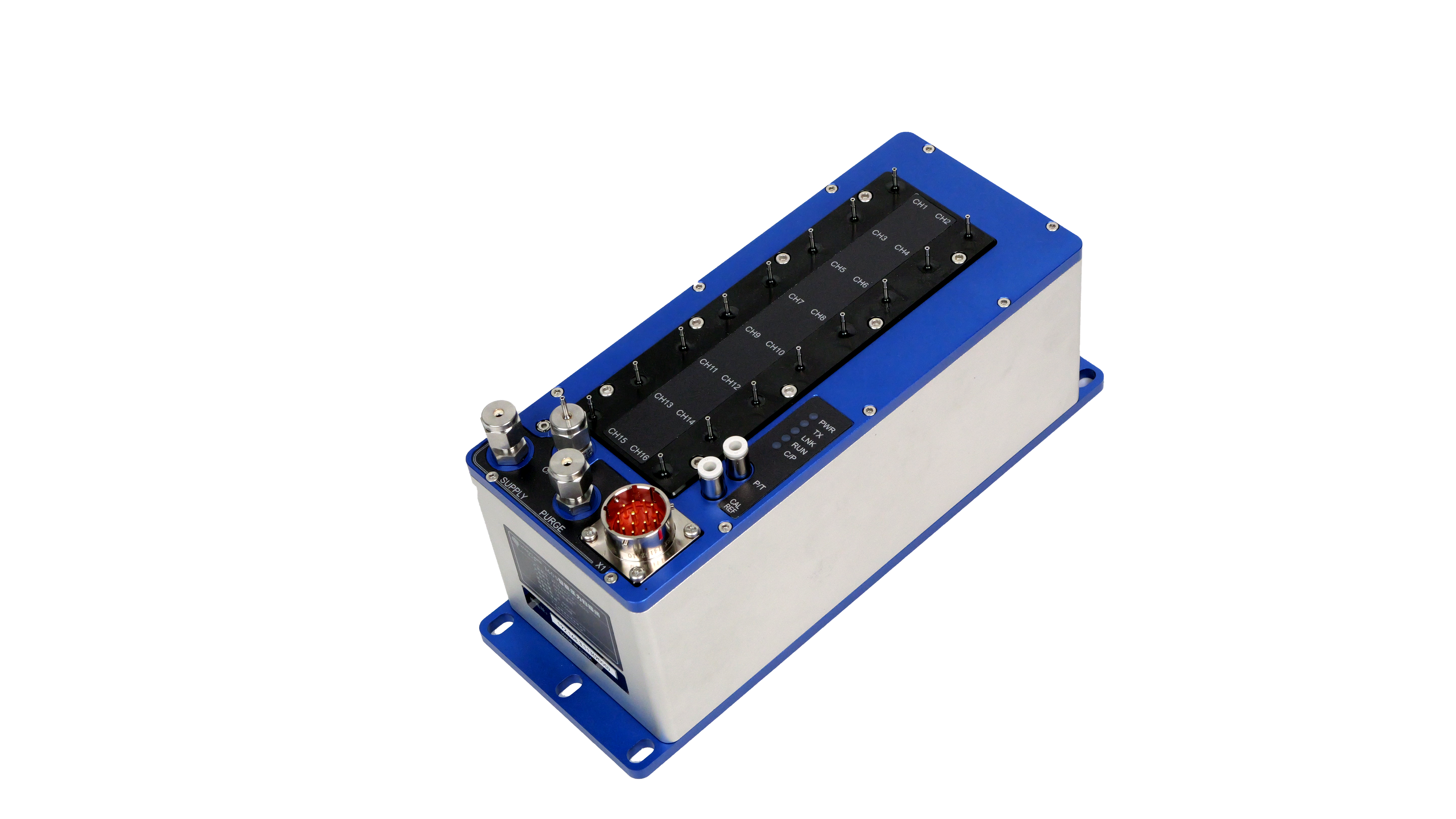
3. Integrated solutions: Reduce system complexity
The WindtunerEthernet Intelligent Pressure Scanners breaks through the limitation of a single pressure measurement function and supports the synchronous collection of multiple physical quantities such as pressure, temperature and displacement through modular design. For example, calculate the thermal stress of turbine blades by combining pressure and temperature data, or analyze the expansion deformation of the casing through displacement signals. This integrated capability simplifies the test bench architecture and reduces the number of sensors and wiring costs.
In the test of a certain type of Marine gas turbine, by synchronously collecting the pressure and temperature data at the turbine outlet and combining with the CFD simulation model, this equipment reduced the calculation error of turbine efficiency from ±2% to ±0.5%. It supports network interfaces of TCP/IP and UDP protocols, which can be seamlessly integrated with upper computers, PLCS and other systems to achieve remote monitoring and automatic analysis of test data.
4. Technological Evolution and Industry Impact
In recent years, the multiple upgrades of the Ethernet Intelligent Pressure Scanners have marked the transformation of the pressure scanning valve from a single pressure measurement tool to an intelligent sensing platform. Its precise time protocol, NTP network time protocol server and automatic startup function make it more adaptable to the testing requirements of the Industry 4.0 era. For example, in the distributed turbine test system, multiple WindtunerEthernet Intelligent Pressure Scanners devices can achieve cross-regional clock synchronization through the NTP protocol, providing a unified time reference for global collaborative research and development.
At present, the technology of pressure scanning valves is developing towards miniaturization and wirelessly. A certain manufacturer has launched a micro pressure scanning valve based on MEMS technology, with a measurement range covering 0.36psi to 1000psi, etc. It can also be customized for a wider range according to the actual needs of users. The weight is reduced by 60% compared with traditional equipment. In the future, with the embedding of AI algorithms, pressure scanning valves will possess self-learning diagnostic capabilities, further promoting the improvement of turbine R&D efficiency and reliability.
The value of the pressure scanning valve in the turbine test bench lies not only in the accuracy and efficiency of data collection, but also in its promotion of the intelligent transformation of testing technology. From dynamic flow field monitoring to intelligent fault diagnosis, from single pressure measurement to multi-physical quantity integrated analysis, this device is becoming the core driving force for turbine research and development innovation.