The reason why pneumatic probes must be calibrated mainly lies in the fact that their measurement relies on the highly coupled relationship between the differential pressure value and the pneumatic Angle. Typical structures such as five-hole probes and seven-hole probes rely on multiple hole positions distributed at the front end of the probe. During the airflow bypass process, different hole openings will experience aerodynamic pressures in different directions. After these pressures are converted through the aerodynamic model, parameters such as static pressure, dynamic pressure, Angle of attack (AOA), and side slip Angle (AOS) are derived. However, in reality, due to manufacturing process errors of the probe, installation Angle deviations, aerodynamic deformation or flow field distortion, there will be deviations between theoretical calculations and actual measurements. The purpose of calibration is to establish an accurate "input-output" mapping model, and to establish a quantifiable and correctable relationship between the original signal of the sensor and the physical quantities of the real flow field.
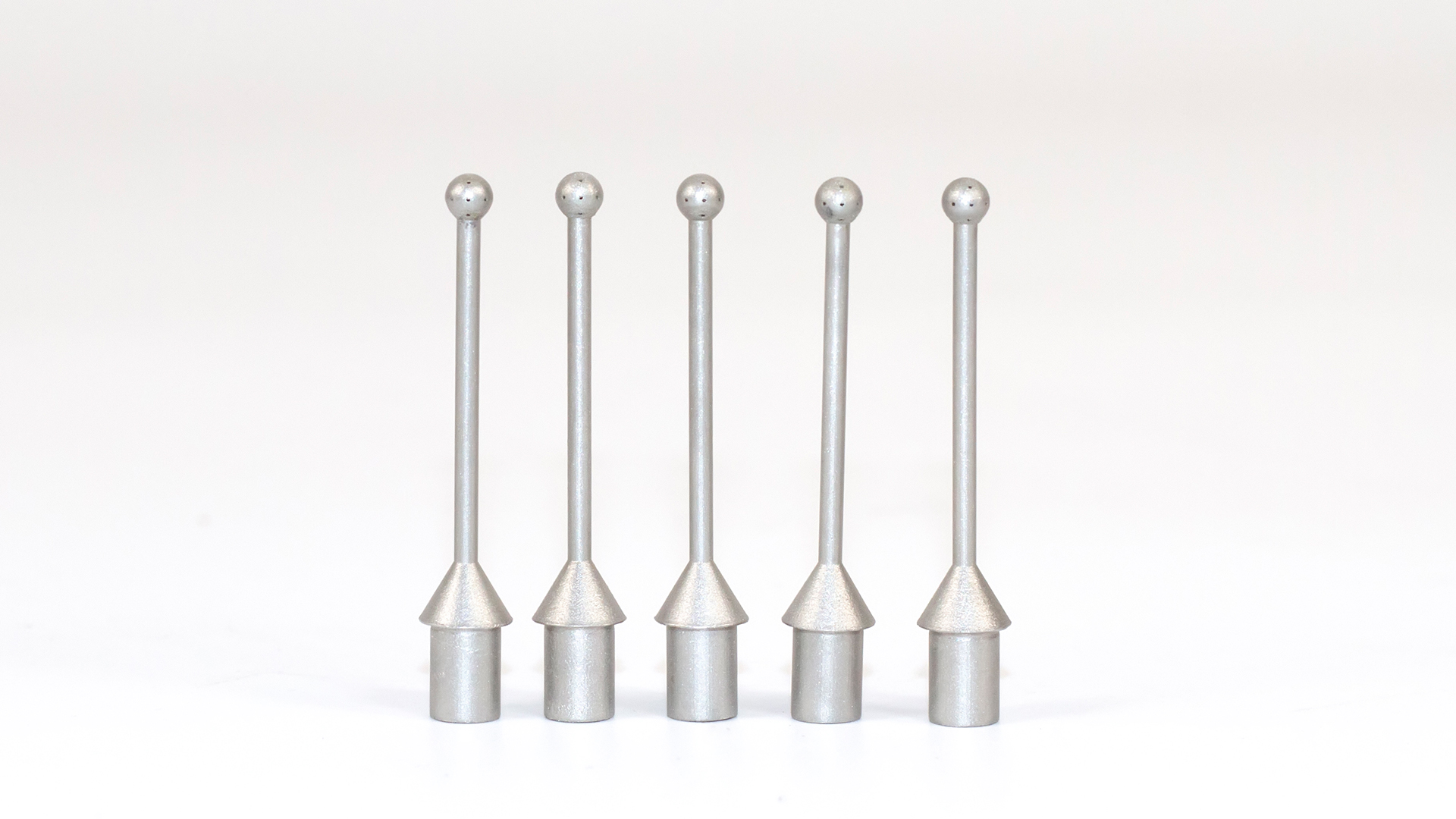
The calibration of pneumatic probes usually needs to be completed in a professional calibration wind tunnel. In this type of wind tunnel, the Mach number, Angle of attack, sideshow Angle and other boundary conditions of the flow field can be artificially controlled, enabling the pneumatic probe to conduct multi-condition tests under controllable, stable and repeatable conditions. Interpolation models or regression models are established through a large amount of sampling data, thereby forming lookup tables or function expressions for measurement parameters. Especially in the application of five-hole or seven-hole probes, nonlinear multi-dimensional calibration algorithms, such as variable Mach number asymmetric interpolation, three-dimensional flow Angle domain fitting and other advanced methods, also need to be introduced to ensure the data accuracy in complex aerodynamic environments.
Take Windtuner as an example. The calibration wind tunnel laboratory built by this company is the first privately-owned wind tunnel calibration experimental platform in China to be certified by CNAS (National Accreditation Service for Conformity Assessment), and it has a management system and testing capabilities that fully comply with international standards. And after professional calibration and testing by the Global Aviation Industry Aerodynamics Research Institute, it was verified that the stability and uniformity of the flow field at the subtransonic nozzle outlet of this wind tunnel fully comply with the national military standard GJB1179A-2012 "Quality Requirements for Flow Field in Low-Speed and High-speed Wind Tunnels". The pneumatic probes calibrated by the Windtunercalibration wind tunnel laboratory can play a stable role in various typical flow fields, which also confirms that Windtuner Technology has the ability to support the requirements of scientific research-level tasks.
Furthermore, an important part of the calibration process is the "recovery characteristic" test. For components such as temperature sensors and pressure scanning valves that work in conjunction with pneumatic probes, as their exposure to high-speed airflow can cause dynamic distortion in heat conduction and sensor response, it is necessary to simulate the actual flight environment through wind tunnels to correct their dynamic response characteristics and calibrate the deviation values under different Mach numbers and attack angles, so as to achieve the data closed loop of the entire pneumatic measurement system.
From the application perspective, uncalibrated probes may perform well under small Angle of attack conditions. However, once they enter complex flow areas, such as the air intake, around the radome, or in high Angle of attack flight states, their nonlinear response characteristics will become significant, thereby expanding the attitude calculation error and affecting the stable operation of the flight control system and the data acquisition system. Especially in fields such as unmanned aerial vehicles, missiles, test aircraft and hypersonic platforms, calibrated probes are a prerequisite for achieving precise restoration of multi-channel aerodynamic data.
Therefore, the calibration of pneumatic probes is not only a fundamental task but also a core link to ensure the authenticity and reliability of aircraft data. It determines the accuracy of the aerodynamic model and also the safety factor of the flight test. In the current era when pneumatic measurement and control is continuously moving towards precision and intelligence, enterprises like Windtuner Technology have established high-standard and full-chain calibration systems. They not only provide reliable testing tools for the industry but also promote China's aviation industry to a higher level through research-level service platforms.